Constrained Supply Chains: Everything You Need to Know
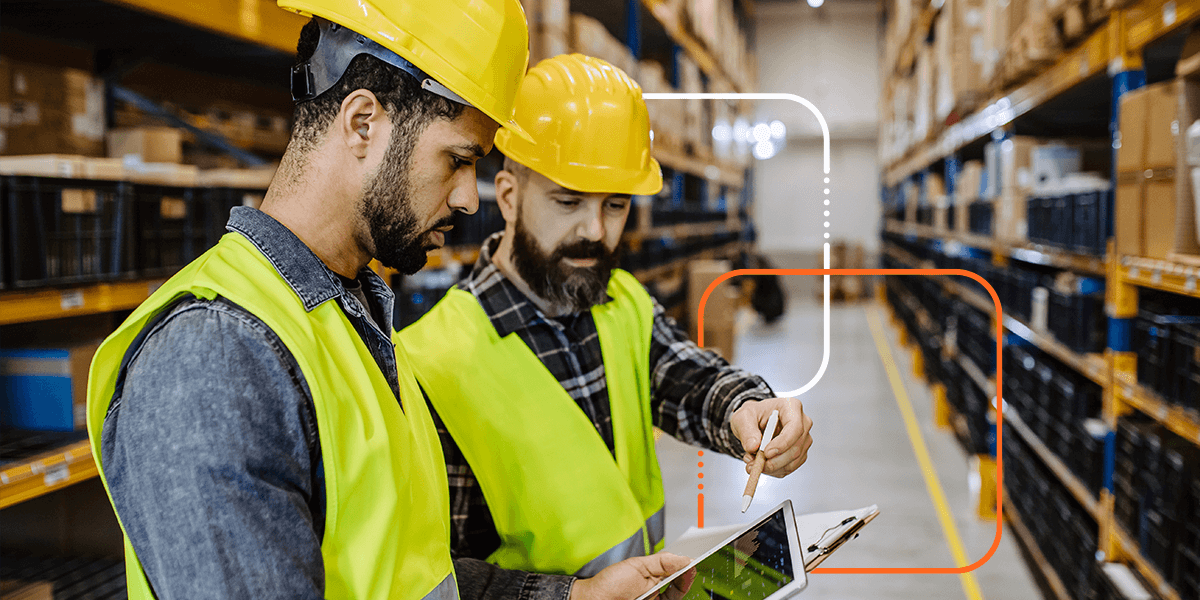
November 29, 2023
Concerns of financial instability and inflation make supply chain management more challenging. By March 2023, prices had increased by 5% compared to the previous year, forcing supply chain managers to work with limited resources. As fears of recession grow, managers must adjust their approaches to meet customer demands with less income.
Constrained supply chains are restricted from working at full efficiency due to various limitations. Constraints could occur during manufacturing, shipping, or daily operations. They can restrict cash flows, productivity, communication, and other crucial operational tasks.
The current economic uncertainty causes many constraints within the supply chain, which could worsen if it progresses into a recession. Officials can limit negative impacts and optimize efficiency with limited resources by building comprehensive response plans.
What Is a Constrained Supply Chain?
A constrained supply chain means companies operate with limited resources and functionality. Businesses don’t have sufficient materials to meet current demand, which results in stock-outs, lost profits, dissatisfied consumers, and other detrimental effects.
When demand outweighs supply, all stages of the supply chain suffer. Companies need to fulfill orders and meet consumer demands to stay profitable. Without the necessary materials, processing orders or maintaining healthy product cycles becomes impossible.
Anything from staff shortages to floods can restrict supply chain operations. These restrictions can cause production delays, poor cash flows, transportation disruptions, and other adverse outcomes. Managers are pressured to meet the same deadlines and demands, but their limited resources make it more challenging to achieve typical business goals.
What Causes a Constrained Supply Chain?
Various problems can become stronger over time and cause long-term harm to the supply chain, including the following:
- Rising costs: Inflation has adverse effects worldwide. As prices increase, it becomes harder for companies to access the resources and services they need for operation. To keep up with rising costs, companies could cut back on resources but still try to operate at full efficiency. This approach can lead to missed production deadlines and employees feeling burnt out.
- Tight job markets: When the number of jobs available is higher than the number of people looking for work, it causes severe constraints on supply chain productivity. Businesses have more difficulty meeting typical consumer demands if they have staff shortages.
- Travel restrictions: International travel restrictions prevent shipments from arriving on time. They can also limit international workers from filling vacant positions.
- Material shortages: If demand rises for specific products, obtaining the necessary materials for their production can become challenging. Raw materials could increase in price, limiting business finances even further. Without enough raw materials, it becomes difficult to produce items at a consistent pace.
What Are Examples of Supply Chain Constraints?
Supply chain constraints can occur at any stage of product movement. Operations consist of four categories — production, distribution, storage, and finances.
1. Production Constraints
Production constraints happen during regular business operations. The constraints could originate during your company’s production processes or occur in other businesses in your supply chain.
Examples of production constraints include the following:
- Machine operations: Many manufacturers use specialized machinery to create or package products. The supply chain needs efficient and reliable machinery to meet order fulfillment requests. However, the equipment could experience downtime that restricts operational efficiency. For instance, technicians could need to turn off a machine during maintenance. Broken parts or machine failure can negatively impact production if companies don’t keep backup machines.
- Staffing levels: Supply chain businesses rely on employees to meet production deadlines, manage finances, respond to customer inquiries, transport products, plan marketing strategies, and complete many other essential operational tasks. Manufacturing labor shortages are unfortunately frequent, with estimates projecting over 2 million unfilled jobs by 2030. Labor shortages can limit these goals and make it harder to work at maximum efficiency. A lack of employees can create additional work for existing team members, increasing feelings of dissatisfaction and burnout.
- Employee performance: Employee errors, scheduling conflicts, or absences could prevent optimal efficiency in your business. Proper training and error correction are crucial for building a responsive and resilient supply chain.
- Workflow efficiency: Your internal procedures can also cause constraints if they waste time or limit productivity. For instance, a workflow with several repeated steps could reduce efficiency rather than boost it.
2. Distribution Constraints
Distribution constraints occur when products move to different points in the supply chain. As shipments pass through the supply chain, they could face obstacles due to factors such as:
- Weather conditions: Adverse weather conditions can make it more difficult to transport products and raw materials. Severe weather, such as flooding or heavy snow, can block roadways or make air travel impossible. Prolonged flooding or snow could also damage inventory stores. Some regions face harsher or more frequent weather threats, such as communities closer to bodies of water or in hurricane-prone areas.
- Transport limitations: The supply chain relies on trucks, planes, and boats to carry shipments. Distribution can face delays if there aren’t enough vehicles or operators. Other external constraints, such as road closures, can prevent vehicles from reaching their destination on time. These situations limit your company’s ability to resolve the problem.
3. Storage Constraints
Supply chain officials who manage product inventory can also experience constraints with storage. Managers need a secure environment to store products but could face various limitations, including the following:
- High costs: Warehouse costs usually depend on the amount of space you use. If you have large products or need to keep significant quantities, storage expenses can quickly rise. Improper inventory management techniques can also cause more constraints. Incorrect forecasting can cause under- or over-stocking, leading to other financial issues. Advanced allocation and visibility methods help you thoroughly trace products and keep a more accurate inventory count.
- Facility capacities: Storage facilities have finite amounts of space. Many warehouses house inventory for multiple companies, limiting space even further. Businesses must optimize their available space and resources, which can become challenging when managing larger shipments or increases in demand. If they need more room, companies must pay higher costs each month.
4. Financial Constraints
Companies must meet customer and supplier demands while maintaining the lowest operational costs possible. Balancing these two goals often causes financial constraints such as:
- Demand changes: Sudden changes in consumer demand can cause financial difficulties across the supply chain. You must have enough funds to order more stock and pay for the necessary storage space. If consumers suddenly lose interest in an item, the existing stock could go to waste, resulting in lost profits. Businesses have to navigate these constraints to meet customer demands but may find their current cash flows can’t accommodate the changes. Demand alterations can also increase costs for raw materials or make it harder to acquire them.
- Cash flows: Healthy revenue cycles keep your company functioning at its best. Metrics such as days sales outstanding (DSO) provide insights into your cash flows, with high DSO numbers indicating unhealthy financial flows. The longer it takes for customers and suppliers to pay, the less cash you will have on hand. You need sufficient cash to cover operational expenses, pay for new stock, compensate employees, and perform other essential tasks. Poor cash flows limit a company’s functionality.
- General expenses: Companies must cover general expenses for supplies, manufacturing processes, storage spaces, and other operational costs. They are also limited by worldwide financial difficulties, such as rising inflation rates. As costs for general expenses increase, businesses could struggle to manage finances. These restrictions make investing in new software, upgrading facilities, or navigating changing customer demands harder.
How Can Supply Chain Managers Navigate Constrained Supply Chains?
Supply chain constraints often occur because of external factors. It is challenging to predict many external challenges due to sudden onsets and a lack of control. For instance, abrupt adverse weather conditions are difficult to predict, making it harder to respond quickly.
Due to the lack of options, officials in constrained supply chains could be forced to prioritize certain goals over others. Navigating many obstacles at once can quickly drain resources.
By altering various approaches, managers can become more equipped to respond to supply chain constraints. Different techniques help you anticipate constraints and build proactive response plans.
These are three ways managers can manage supply chain constraints:
1. Identify Operational Bottlenecks
Increased visibility can help you identify potential constraints before they occur. Steady flows of parts and materials let you proceed with operations according to original estimates and timelines. By looking at an end-to-end view of your operations, you can notice bottlenecks or potential areas for concern.
You could use supplier mapping to build a complete portrait of suppliers, products, parts, and distribution paths. For each supplier, consider factors such as:
- Inventory levels
- Facility locations
- Products or parts made
- Level of part importance for your operations
- Typical operational times or capacities
- Average distribution times
The comprehensive map gives more insight into bottlenecks or inefficient areas. With a clearer image of these potential disruptions, supply chain managers can build response plans in case constraints occur.
For instance, you may notice the distance between your facility and a supplier’s facility creates more transportation limitations. If you consistently receive late shipments because of terrain obstacles, you could rework your shipment procedures to address these concerns. You might switch to a local supplier or establish a backup relationship in case the first option can’t meet your deadline.
It also helps to consider which constraints impact your company the most. Disruptions vary by company location, financial circumstances, staffing levels, and other specific factors. Addressing the most frequent or severe limitations can minimize negative effects. While external factors such as weather conditions or market instabilities are out of your control, you can adjust internal procedures to reduce disruptions.
For example, you could implement new credit checks or streamline invoice processing to reduce DSO. Or if you notice employee errors are a common constraint cause, you could begin new training initiatives.
2. Use Demand Forecasting
Demand forecasting increases your company’s agility and resilience. Data-driven insights into buying patterns, product prices, distribution times, and other crucial metrics help companies make more informed decisions. Predicting upcoming trends lets you prepare for possible constraints instead of responding in the moment.
Advanced forecasting tools increase accuracy and create more digestible data. If your forecasting insights are often inaccurate or unhelpful, switching approaches can help you optimize results. For instance, automation can streamline and enhance demand forecasting. Automated software monitors inventory levels and previous order details, then generates replenishment recommendations. It also provides real-time data for buying patterns and ongoing disruptions, allowing you to react swiftly.
The more prepared you are for constraints, the more you can minimize their effects. For example, a prediction tool could forecast an abrupt surge in demand for a product. You could increase your order quantity to ensure you meet the upcoming change. You could also optimize available storage space to fit the larger quantities.
Companies can also prepare for external constraints with additional forecasting research. Severe weather situations such as hurricanes, tornadoes, or floods can significantly impede supply chain processes. You can take proactive measures by stocking additional inventory when these seasons approach, or you could diversify your suppliers by establishing partnerships in areas with fewer weather impacts.
3. Upgrade Your Technology
Your company’s technology directly affects efficiency and accuracy. Often, outdated systems cannot support modern constraints and demands. You might face difficulties with data transfers, loading times, or integrating applications. An updated software solution can help you anticipate and respond to various supply chain constraints. It prepares you to remain agile when facing limitations.
For example, Vendor Managed Inventory (VMI) and Electronic Data Interchange (EDI) are two integrated solutions that can enhance your response to supply chain constraints.
VMI provides real-time inventory data and replenishment recommendations. It considers unique business circumstances and recommends the best reordering strategies. VMI also eases collaborations between partners by automatically syncing data across different platforms. Even amidst supply chain constraints, the solution uses deep data and historical insights to recommend the best path forward.
EDI streamlines document exchanges between suppliers and stakeholders. Reduce manual errors and streamline communication with instant data transfers. Effective communication creates a more unified supply chain — you can keep others updated on ongoing or potential constraints, limiting negative effects.
You can adopt several solutions to develop end-to-end preparation for disruptions and constraints. Software providers can recommend the best solution for your company’s needs and preferences.
Use VMI and EDI to Manage Supply Chain Constraints
Internal and external constraints restrict companies from performing at top efficiency. In response, you could face lost profits, strained supplier relationships, dissatisfied customers, or various other negative impacts. While you can’t avoid constraints altogether, your company can invest in tools that prepare you to respond more effectively.
Software solutions such as VMI and EDI give you the necessary tools to build supply chain resilience. Automation eliminates many manual tasks, boosting efficiency across your operations. Data-backed insights let you make the most informed decisions about factors from replenishment to marketing approaches.
To learn more about how our VMI and EDI solutions can assist with supply chain constraints, contact TrueCommerce today.
Check out the IDC MarketScape: Worldwide Multi-Enterprise Supply Chain Network (MESCCN) 2023 Vendor Assessment where TrueCommerce is recognized as a Leader.
Share this post:
Stay ahead of the competition
Get expert supply chain insights delivered directly to your inbox weekly.