Deep Dive: How Dock Scheduling Reduces Detention and Per Diem Fees
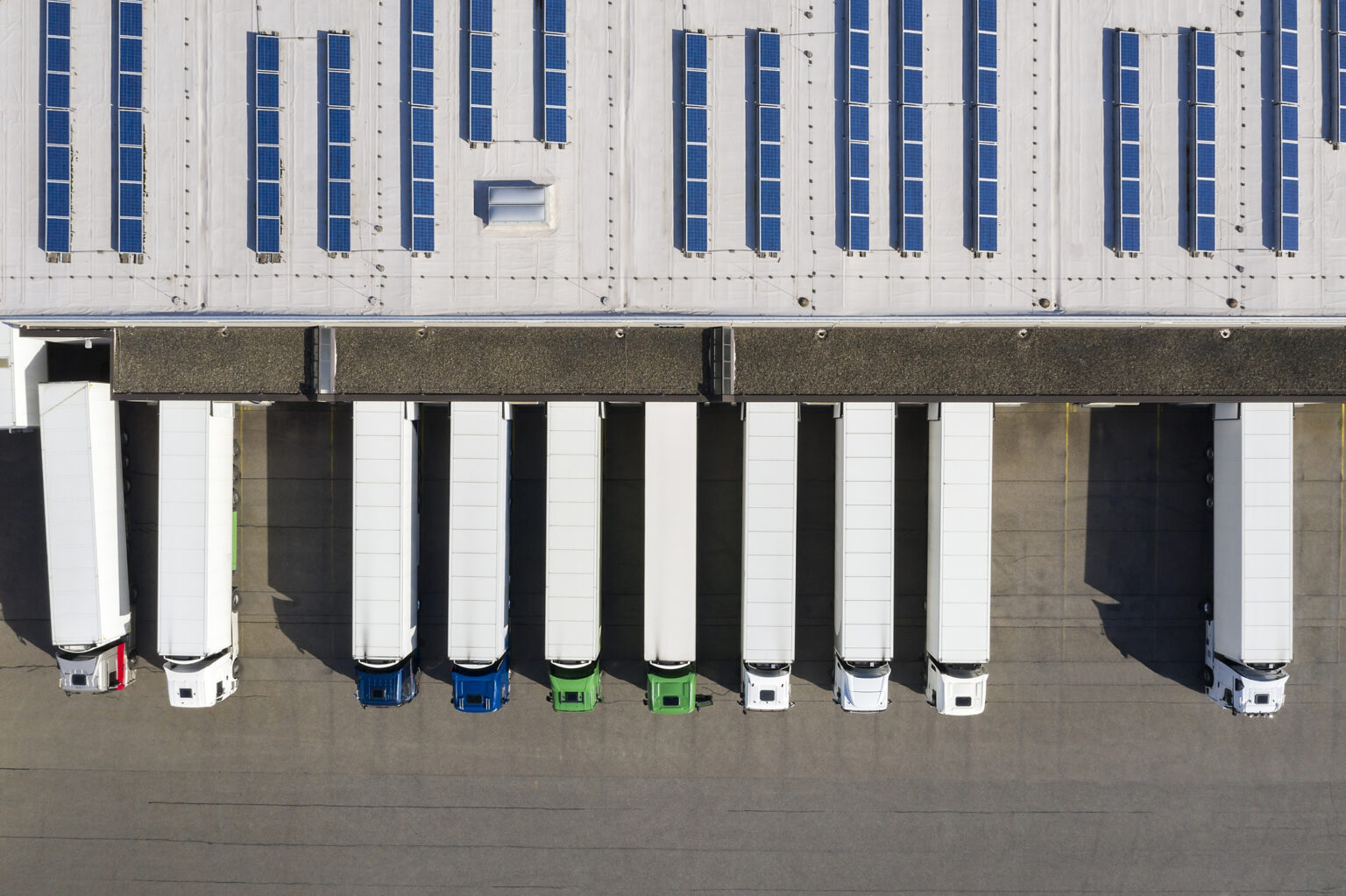
March 27, 2020
Three things that thousands of retailers, warehouses, and distributors have in common? Congested docks, overworked employees, and too much paperwork. Between managing dock appointments, accounting for surges in deliveries, and making sure the right people are in place, keeping a “clean” yard seems like a pipe dream to many in the warehousing industry.
To add to the burden of an already difficult task, the delays caused by warehouse inefficiencies have another bit of fallout: late fees. Detention and per diem fees are terms that leave many dock managers and business owners feeling queasy, and for good reason. Dock fees can add up to hundreds of dollars per carriage per day– which adds up to hundreds of thousands of dollars per year.
Dock scheduling software aims to solve these problems by giving managers easy ways to visualize and plan ahead, suppliers the ability to make their own appointments, and workers the tools they need to handle inbound and outbound loads effectively.
Detention and Per Diem Fees Explained
Before getting into ways of reducing costs, it’s important to understand the different types of fees you may incur in your dock and yard. Generally, there are two types of fees you’ll encounter in this area: detention and per diem fees.
Detention fees are costs incurred when a trucker has to wait in your yard for docking, or at the door to be unloaded, past their predetermined “free time.” Generally, truckers and their employers can ask for anywhere from $50-$100 per hour to cover this extra time. Remember, time spent at your dock is not only time your truck partners are spending off the road (truckers are paid by the mile, not by the hour), but may also impact important scheduling for off time, such as necessary sleep hours.
Per diem fees relate to the shipping container, or carriage, itself. After unloading, the receiving warehouse has a set number of days to return the empty carriage– usually 4-5 business days. When that time runs out, the receiver begins to incur a daily fee (hence the name “per diem”). These fees can average around $150 per day per container; however, specific fees will differ from supplier to supplier and may be subject to increases depending on how late you are with your returns.
How to Slash Late Fees with Dock Scheduling
A few hours of a trucker’s time or a few extra days with a container may not seem like a huge loss. But I’ll give you two thoughts to mull over in that regard. First, as a business owner, any loss counts against your net revenue, so it’s just good business sense to try to minimize or eliminate late fees.
Second, while the fees may be insignificant for a small two- or three-door dock that receives a couple of shipments per week, larger organizations with many docks that receive multiple daily shipments will realize a much bigger impact. In addition to a larger number of fees, these businesses experience a higher likelihood of inadequate carriage tracking, which means a higher rate of increase in the fees over time.
Plan Strategically with a Calendar View
If you’re anything like most warehouse owners, chances are that the mention of excel sheets and hand-written schedules immediately increases your blood pressure. And yet, for many dock managers, these seemingly archaic practices are still the status quo. Not only does this mean doing all your scheduling by hand, which eats up man-hours by the dozen; it also leads to miscommunications, human errors, and delays that result in late fees.
Our dock scheduling software solves these problems in myriad ways. First off, the calendar view on our ecUtopia module makes it easy to see which shipments are arriving when, so you can plan accordingly. Second, the visual view of your yard makes it easy to see the flow of your yard throughout the day, which can help you to strategically choose door and dock assignments that reduce congestion and backups.
Third, and perhaps more importantly, is that dock scheduling software allows you to quite literally make the rules. From choosing which partners can make appointments, to limiting the number of appointments per door, to designating open, closed and blocked times for each door, the rules you set let you customize your calendar for the highest rates of efficiency– and therefore the lowest possibility of fee incurrence.
Reduce Congestion by Empowering Suppliers
It seems like dock managers spend half their time on the phone, helping their suppliers make dock appointments. With dock scheduling, your suppliers are able to access the schedule remotely via our web portal and see available time slots, so they can also plan ahead. Trusted suppliers can make a dock appointment directly in the portal, and update the appointment if arrival times or other details necessitate an appointment change. All the information is updated automatically for the dock manager, so they have an up-to-the-minute accurate view of their schedule.
The result? Because your suppliers can make and update appointments based on real-time data, your dock is prepared for changes in your schedule that would otherwise lead to congestion and gridlock. And with less congestion, incoming loads will have shorter wait times and faster unload times. This not only means fewer late fees on a per truckload basis– it also puts an end to the snowball effect where one delay in the day turns into a dozen more.
Enable Your Staff to Work Efficiently
Your dock manager might be spending hours on the phone with customers and adjusting their schedule sheets, but they aren’t the only staff members affected by outdated dock scheduling. Dock workers often find themselves at the mercy of unpredictable days; staff shortages during surges mean slower unloading, more delays, and overtime work, while slow days mean hours with very little to do. For the sake of detention fees, let’s focus on those busy days, and how scheduling software can help.
For dock managers, less time spent trying to get that excel spreadsheet in order means more time that can be spent on managing employees. The clarity provided by a constantly updated dock schedule view can help your managers determine appropriate staffing numbers ahead of time, ensuring that each carriage is unloaded efficiently, without the need to rush or overwork your staff. The right workers in the right place at the right time greatly increases your ability to unload each carriage in a timely manner, so your trucking partners can quickly be on their way.
For dock workers, access to the schedule from mobile devices or tablets keeps your employees informed and updated on incoming loads. This communication, paired with better staffing plans, results in less stress and more teamwork, which can help maintain efficiency and reduce mistakes that lead to delays and detention fees.
Keep Your Yard Clean With Container Alerts
One of the biggest causes of per diem fees is simply a lack of tracking. Even containers that arrive and are unloaded in a timely manner could end up sitting idle in your yard for weeks at a time, because no one is keeping a record of when each container’s free time runs out. Some docks with excel sheets, or even clipboard schedules may have this information, but keeping up with those dates across an array of containers can quickly become a time-consuming and overwhelming manual effort, with some containers still falling through the cracks due to human error.
Dock scheduling eliminates this issue by allowing you to set the number of days allowed for returns by the supplier, as dictated by your contracts. The system keeps track of arrival dates and subsequent due dates, and can be set to warn you when a container is nearing its due date. This makes it easy to prioritize and schedule returns to maximize the number of containers that are returned before they incur per diem fees, while at the same time keeping your yard clean and organized, and ready for new shipments.
Take Back Control of Your Yard and Dock
Dock scheduling and yard management aren’t easy, but with the right technology in the hands of your managers, you can create an efficient dock that keeps your shipments flowing, your trading partners happy and your late fees near to zero. And with the money and time you save, you can spend more time and funds giving your company a competitive edge across channels.
Ready to enhance your yard and dock performance? To learn more about TrueCommerce ecUtopia’s dock scheduling module, reach out now. To see how else we can help your company do business in every direction, check out our latest blogs on unified commerce and scan-based trading.
Go Wherever Business Takes You with Unified Commerce from TrueCommerce
Increase sales, decrease costs and get back time in your day with integrated dock scheduling that makes your business more connected, more supported, and more ready for what’s next.
Share this post:
Stay ahead of the competition
Get expert supply chain insights delivered directly to your inbox weekly.