Transforming Manufacturing: Exploring the Benefits of the Connected Factory
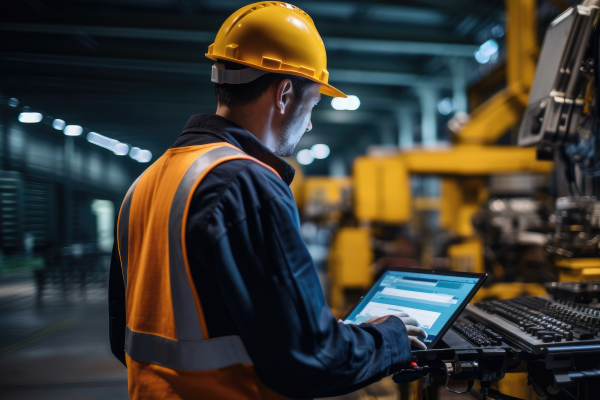
December 12, 2023
What is The Connected Factory?
The Connected Factory isn’t a new term. Traditionally, it refers to a smart manufacturing facility that utilizes digital technology to enable seamless and automated information sharing between people and machines. The fundamental idea behind the Connected Factory is to create a highly interconnected digital supply chain and encourage accountability at all levels of the supply chain process. It also allows for a comprehensive view of inventory placement across the supply chain, enabling each smart factory to be better prepared for potential shortages of components.
Benefits of Digital Connectivity in Supply Chain
By having this view, operational guidelines can be established around projected part scarcities, and potential line stoppages can be foreseen. The Connected Factory concept uses digital interlinking to connect all tiers of suppliers, Original Equipment Manufacturers (OEMs), and manufacturers, resulting in real-time insights into inventory levels, production workflows, and possible interruptions. Having this digital connectivity facilitates communication and data exchange, which leads to multiple advantages such as:
- Improved Supply Chain Visibility: Seamless digital interconnection across every stage of the supply chain provides manufacturers with uninterrupted access to real-time data concerning inventory levels, production advancement, and transportation status. This heightened transparency empowers them to make decisively informed choices and swiftly adapt to dynamic shifts or unexpected interruptions.
- Proactive Planning: The Connected Factory methodology enables businesses to foresee and effectively strategize for potential shortages or disruptions in parts. With an all-encompassing view of inventory levels and production schedules, companies gain the capacity to fine-tune their manufacturing processes proactively, thus reducing downtime and preventing line stoppages.
- Enhanced Inventory Management: The real-time data and analytics offered by the Connected Factory initiative improve inventory management. This empowers manufacturers to adequately adjust their inventory levels, effectively mitigating surplus stock while ensuring a sufficient supply of components readily available to fulfill production requirements.
- Business Rule Automation: Manufacturers can automate specific operations, such as reordering parts once inventory levels reach a predetermined threshold. This automation not only fosters operational efficiency but also serves as a robust safeguard against potential human errors.
- Supply Chain Optimization: Manufacturers can also forge heightened integration and seamlessness within their supply chain by utilizing the Connected Factory concept. It allows them to pinpoint bottlenecks, rectify inefficiencies, and capitalize on opportunities for refinement, resulting in finely tuned processes and notable cost reductions.
- Collaboration and Data Sharing: Integrating all stakeholders through digital connectivity enhances collaboration and efficiency. The exchange of data among OEMs and suppliers cultivates a synergistic and adaptable ecosystem within the supply chain.
Fostering an Inclusive Community of Diverse Partners
To ensure the success of the Connected Factory concept, it is crucial to cultivate an inclusive community of diverse partners. This requires proactively fostering an environment that embraces and interconnects with various trading partners and networks, including:
- Suppliers who provide direct and indirect goods and services to purchasing organizations
- Manufacturers responsible for producing components, packaging, or any other elements used in a company’s products
- Logistic experts, carriers, and shippers who manage the transportation of raw materials to a company and the distribution of final products to customers
- Solution providers that enrich transactional and operational data with valuable insights and context, thereby improving assessments, decisions, and planning.
- Physical assets, such as machinery on a production floor or equipment capable of providing data to enhance workflow and process efficiency, whose performance directly influences business outcomes.
- Existing networks that explore opportunities to integrate with other networks, including freight networks. This can help consolidate access to multiple service providers or tap into established suppliers, logistics, assets, or other networks.
By collaborating with diverse partners and networks, companies can ensure the vitality of the Connected Factory concept and drive business success.
To learn more about the Connected Factory and how it can apply to specific industries (particularly the automotive industry), read our whitepaper, The Connected Factory Concept.
Building a Digital Supply Chain for Automotive with TrueCommerce
TrueCommerce is helping auto companies digitize their supply chain with our automotive solutions.
TrueAuto is an iPaaS B2B solution designed to digitize an automotive manufacturer, from the largest OEM to the smallest Tier supplier. Working together with existing technologies and systems, TrueAuto provides the necessary functionality to proactively manage the automotive supply chain and achieve compliance in accordance with industry best practices. We simplify mapping, replacement logic, and reconciliation, creating a simple and efficient process.
When it comes to clean data, ensures quick access to impactful data and acts as a filter between the end user’s systems and their customers. Additionally, TrueAuto adheres to compliance standards within the industry, including MMOG/LE, and is Honda approved. All of this is conducted within the cloud utilizing our fully managed service. Contact us today to learn more!
Share this post:
Stay ahead of the competition
Get expert supply chain insights delivered directly to your inbox weekly.