The Connected Factory: Digitally Connecting the Automotive Supply Chain
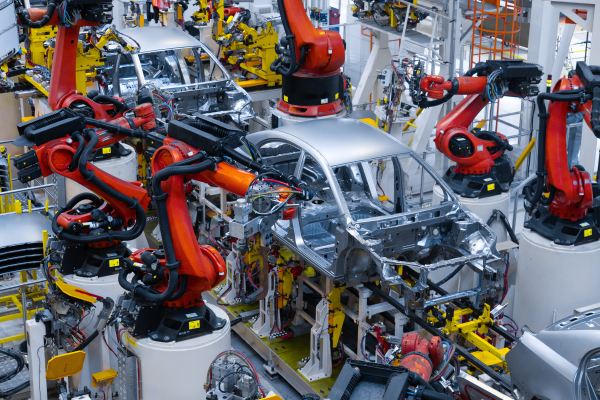
December 20, 2023
In a recent blog, we outlined the Connected Factory Concept and how it refers to a smart manufacturing facility that utilizes digital technology to enable seamless and automated information sharing between people and machines. The fundamental idea behind the Connected Factory is to create a highly interconnected digital supply chain and encourage accountability at all levels of the process.
The intricate supply chain of the automotive industry extends across multiple tiers of global suppliers. The onset of the pandemic resulted in significant disruptions to production and distribution, leading to critical shortages of essential components like semiconductors (chips) crucial for modern vehicles.
Consider the application of the Connected Factory Concept to the automotive supply chain. This approach would establish a seamless digital thread connecting Original Equipment Manufacturers (OEMs) with Tier 1 suppliers, who in turn connect with Tier 2 and 3 suppliers, creating a continuous flow of information throughout the entire supply chain.
The automotive industry faces several challenges that require adaptation and significant investments in operational frameworks to establish heightened resilience within its supply chains. Fortunately, the Connected Factory process can link factories and manufacturing facilities in real-time, providing visibility into the production capacity of trading partners and available inventories.
This integration also provides valuable insights, enabling manufacturers to strategically align production rates and mitigate any deviations in output. Additionally, the data facilitates comprehensive risk analysis and insights into the precise whereabouts of crucial raw materials or components within the supply chain, all while simplifying complex automotive supply chain procedures through automation.
The Connected Factory concept not only enhances operational efficiency, but also transforms disruptions into opportunities for efficient delivery and intelligent collaboration across the entire trading community.
- Supplier Diversification: The transformation of the automotive industry’s fragmented supply chain involves implementing various measures. To mitigate risks, automotive OEMs and Tier 1 manufacturers must avoid dependence on a single source for critical components. Instead, fostering partnerships with alternative suppliers across different geographical regions is crucial. These selected partners should possess the technical expertise necessary for seamless digital connectivity.
- Enhanced Supply Chain Visibility and Tracking: Investing in advanced supply chain management technologies is critical for visibility and tracking. This technology provides real-time visibility into the movement of parts and components, empowering OEMs and Tier 1 suppliers to anticipate potential disruptions proactively. This approach eliminates line stoppages and parts shortages, fostering predictability and reducing the reliance on reactive supply chain management.
- Inventory Management: Maintaining a buffer inventory for essential components, in addition to Just-in-Time (JIT), can serve as a safety net during supply chain disruptions. Transitioning from a finite, time-limited JIT approach to a mutually agreed-upon, shared inventory, risk-based strategy (Just-in-Case) is a significant step toward achieving supply chain predictability.
- Collaboration and Communication: Close collaboration and transparent information sharing between OEMs and suppliers is essential to address supply chain challenges collectively. Digital connectivity facilitates bidirectional communication across the entire automotive supply chain, providing a single, accurate source of truth regarding inventory location and arrival times. Extending this digital collaboration to include third-party logistics (3PL) providers and transport companies enables real-time tracking of shipments and their contents.
- Adopting New Manufacturing Technologies: Embracing automation, robotics, and additive manufacturing (3D printing) reduces dependence on specific suppliers and enhances production flexibility. Tracking containers throughout the manufacturing process saves substantial costs and contributes to waste reduction and environmental sustainability. Container tracking allows for reuse, saving billions of dollars in manufacturing.
- Proactive Risk Assessment and Scenario Planning: Regularly evaluating potential risks and developing contingency plans prepares companies for unforeseen events. The true value lies in providing actionable information to planners regarding the whereabouts of parts, minimizing shortages upon their arrival at the manufacturing plant.
- Commitment to Long-term Investments: Recognizing that supply chain improvements require long-term investment and commitment is essential. This commitment may involve infrastructure upgrades, logistics enhancements, and the adoption of new technologies, ultimately paving the way for the implementation of connected factories.
By implementing these strategies, the automotive industry can fortify its supply chains, making them more robust and adaptable to future disruptions. This enhanced resilience will enable the industry to meet customer demands more effectively and ultimately improve profitability. The lessons drawn from the challenges posed by the pandemic should act as a catalyst for positive transformation within the automotive sector.
For a more in-depth view of the Connected Factory and how it applies to various industries, namely the automotive industry, read our whitepaper, The Connected Factory Concept.
Share this post:
Categories
Stay ahead of the competition
Get expert supply chain insights delivered directly to your inbox weekly.